FRASCOLD คอมเพรสเซอร์ลูกสูบ 2 Stage (Semi-Hermetic) รุ่น S-V Series
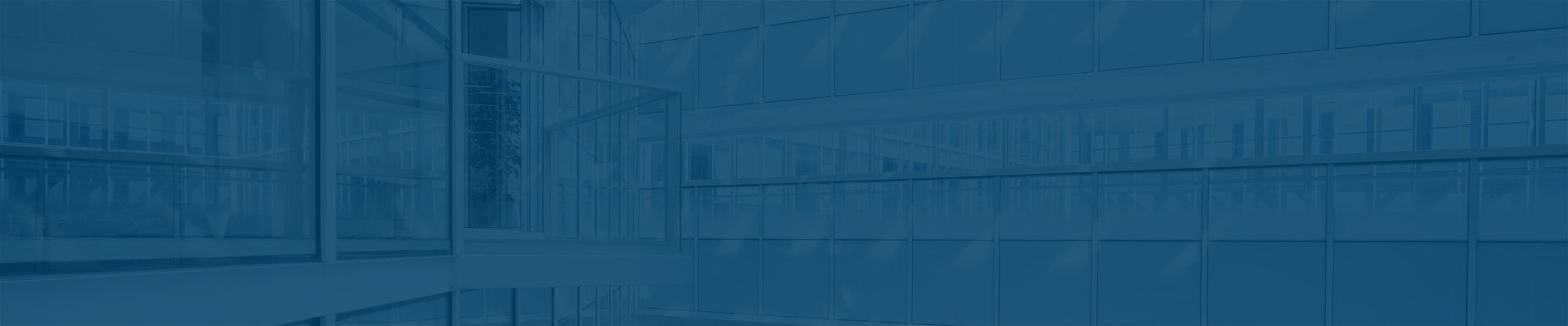
Model | Cylinders [LP,HP] | Displacement LP [50Hz/60Hz] | Displacement HP [50Hz/60Hz] | Oil Charge [dm³] | Add to Cart |
---|---|---|---|---|---|
S5-26.16Y | 2,2 | 25,2/30,24 | 16,39/19,67 | 2,9 | |
S7-27.19Y | 2,2 | 26,85/32,22 | 19,12/22,94 | 2,9 | |
2V10-42.29Y | 2,2 | 41,89/50,27 | 29,4/35,28 | 4 | |
2V15-56.32Y | 2,2 | 56,05/67,26 | 32,04/38,45 | 4 | |
2V20-62.35Y | 2,2 | 61,57/73,88 | 35,2/42,24 | 4 | |
2Z15-60.30Y | 4,2 | 58,81/70,57 | 29,4/35,28 | 7,2 | |
2Z20-72.36Y | 4,2 | 70,74/84,89 | 35,37/42,44 | 7,2 | |
2Z25-84.42Y | 4,2 | 83,77/100,52 | 41,89/50,27 | 7,2 | |
2Z30-102.51Y | 4,2 | 102,86/123,43 | 51,43/61,72 | 7,2 | |
2Z35-112.56Y | 4,2 | 112,11/134,53 | 56,05/67,26 | 7,2 | |
2Z40-123.62Y | 4,2 | 123,13/147,76 | 61,57/73,88 | 7,2 |
ASERCOM CERTIFICATION
What is ASERCOM
ASERCOM (Association of European Refrigeration Component Manufacturers) promotes standards for safety and performance ratings in the refrigeration industry ASERCOM certification means that a compressors performance has been determined to meet the specifications stated by its manufacturer.
How It Works
Manufacturer’s performance data for a particular compressor model and refrigerant are submitted to ASERCOM for certification. To ensure objectivity, members of the certification committee are selected from competing manufacturers. the committee. agrees with the submitted performance data that model is added to the certified list.
Performance Testing
Models from the certified list are regularly tested to verify performance. To ensure fairness, the compressor to be tested is obtained from a distributor’s stock and tested at a competitor’s facility. If test results are not up to the listed specifications that model is removed from the certified list.
FEATURES
- Compact Design : Thanks to the elimination of external conduits, the compressor features reduced dimensions.
- Reliable & Sturdy : The new specially designed components make the compressor resistant to all operating conditions within its working range.
- Sub-cooler Kit : All models can be fitted with a pre-assembled sub-cooler that can be provided installed and connected or supplied separately.
- Optimized Liquid Injection : The compressed gas and injected liquid mixing process is instantaneous and the liquid is not overheated as it does not go through the motor.
- Exclusive motor Cooling System : The motor is injected solely with the exact amount of fluid required to cool the motor. This system, only available on Frascold compressors, prevents the formation of ice on the motor by eliminating damage by oxidation, by condensate in the electrical box and liquid slugging.
- Increased Efficiency : Special bearings have been designed with a cage that helps reduce noise levels and increase the load coefficient and their operating life.
- Silent Operation : Thanks to the dual liquid injection, purposely designed to optimize the operation of the compressor to achieve maximum performance.
MOTOR COOLING SYSTEM
- Constant and accurate control of the motor temperature : The system accurately and constantly checks the temperature via the AMS sensors located inside the wings. Indeed, the position of the sensors has been specifically designed to identify the most critical areas in terms of overheating, thereby allowing to protect the motor also during the critical start-up stage.
- Efficient motor cooling : The system identifies when the pre-alarm temperature threshold is reached and activates the injection of liquid in the motor according to optimized amounts and time.
- Compressor reliability : The controlled cooling of the motor prevents excessive cooling on neighboring areas, eliminating the risk of frost and resulting oxidation, thereby preventing the formation of condensation in the electrical box of the compressor and the risk of a short circuit.
- Prevention of motor overheating : The system identifies when the critical temperature threshold has been reached and stops the compressor in the event of anomalous overheating.
- Liquid injection monitoring : Thanks to the TA (Current transducer used as power ON Sensor) device installed as standard, as well as injecting the liquid as required, the system can prevent this function when the compressor stops due to a malfunction of the compressor itself or due to external system management logics.
*** Remark : Motor power supply 380-420V (Y) / 3ph / 50Hz | 440-480V (Y) / 3ph / 60Hz | PWS Connection
ดูเพิ่มเติม
ดูน้อยลง